Nurul Kabir Minar
Incharge Branch Operations & Distribution
Berger Paints Bangladesh Ltd.
He is an accomplished professional in supply chain and logistics management, currently serves as Incharge of Branch Operations & Distribution at Berger Paints Bangladesh Ltd. With a robust background in Business Administration and extensive experience in overseeing logistics operations, Nurul is recognized for his strategic acumen and dedication to optimizing supply chain efficiency. His leadership has been instrumental in enhancing operational resilience and customer satisfaction, making him a pivotal figure in the chemical industry’s logistics landscape.
The InCAP: Mr. Nurul Kabir Minar, please share your professional and academic peregrination for our readers!
Mr. Nurul Kabir Minar: I completed my Bachelor’s and Master’s degrees in Business Administration with a specialization in Finance from the University of Chittagong. The rigorous academic environment and comprehensive curriculum provided me with a strong foundation in financial principles and their real-world applications. This educational background has been instrumental in my career, enabling me to analyze complex financial scenarios and make informed decisions in my supply chain & logistics roles.
Joining KDS Logistics Ltd. (KDSLL), the largest inland container depot (ICD) and container freight station (CFS) in Bangladesh, was an incredible opportunity. As a Management Trainee Officer, I was exposed to various facets of logistics and supply chain management. The role required coordinating with different departments, managing operations, and ensuring efficient movement of container, connecting with Main Line Operators/Shipping Lines, container repairing sections, sales, transport equipment & fleet operation. This experience was invaluable as it honed my operational and managerial skills, setting a solid foundation for my future career advancements specially working under my mentor, vice president of KDSLL.
When I swiftly was moving up the ranks to Assistant Manager, In pursuit of new challenges and opportunities, I accepted an exciting offer from Berger Paints Bangladesh Limited (BPBL), the market leader in the paint industry leading by our visionary leader, Mrs. Rupali Chowdhury. Joining as Incharge Branch Operations and Distribution in dual roles at a depot, i have been solely working in the supply chain department for the past 4.5 years. This department is renowned for its country best efficiency and prominence and I have had the privilege of contributing to its success working under Head Demand Supply Planning & Manager Customer Service & Distribution by streamlining operations, warehouse management and ensuring customer satisfaction across southern part of Bangladesh. Along with this, I’m also looking after admin, another leading & employee oriented department of Berger paints.
What strategies have you implemented to improve the supply chain and logistics operations at Berger Paints Bangladesh Ltd. during critical situations?
Well, Navigating critical situations in supply chain and logistics requires a combination of strategic planning, adaptability, and innovative thinking what we did.
During critical situations, communication becomes paramount. I facilitated enhanced communication channels between various departments, customers and other logistics partners. Regular updates and transparent communication ensured that everyone was on the same page, enabling swift decision-making and coordinated responses to any issues that arose. One of the foremost strategies has been proactive risk management. By identifying potential risks early on, such as supply chain disruptions, transportation delays, or inventory shortages, BPBL were able to bring accuracy in consensus demand planning. This involved diversifying our supplier & customer base, maintaining safety stock levels, and establishing alternative logistics routes to mitigate the impact of any unforeseen disruptions. Furthermore, Leveraging technology played a significant role in improving our operations. This enabled us to make data-driven decisions, optimize inventory management, and reduce lead times. We adopted an agile approach to our operations, allowing us to quickly adapt to changing circumstances in extreme time such as covid-19 pandemic period. This involved reallocating resources and optimizing our distribution network to ensure timely deliveries. By maintaining a flexible mindset, we were able to respond effectively to sudden changes in demand or supply chain disruptions. During crisis period of our operation, we successfully are going ahead our company associating with diversified technology we have.
Finally, fostering a culture of continuous improvement and investing in employee training has been vital. We regularly conducted training sessions for our team on best practices in supply chain management, crisis management, and problem-solving. Encouraging a proactive approach and empowering our team to identify and implement process improvements have resulted in increased efficiency and resilience.
These strategies have collectively enhanced our supply chain and logistics operations enabling us to maintain high service levels and meet customer expectations even during critical situations.
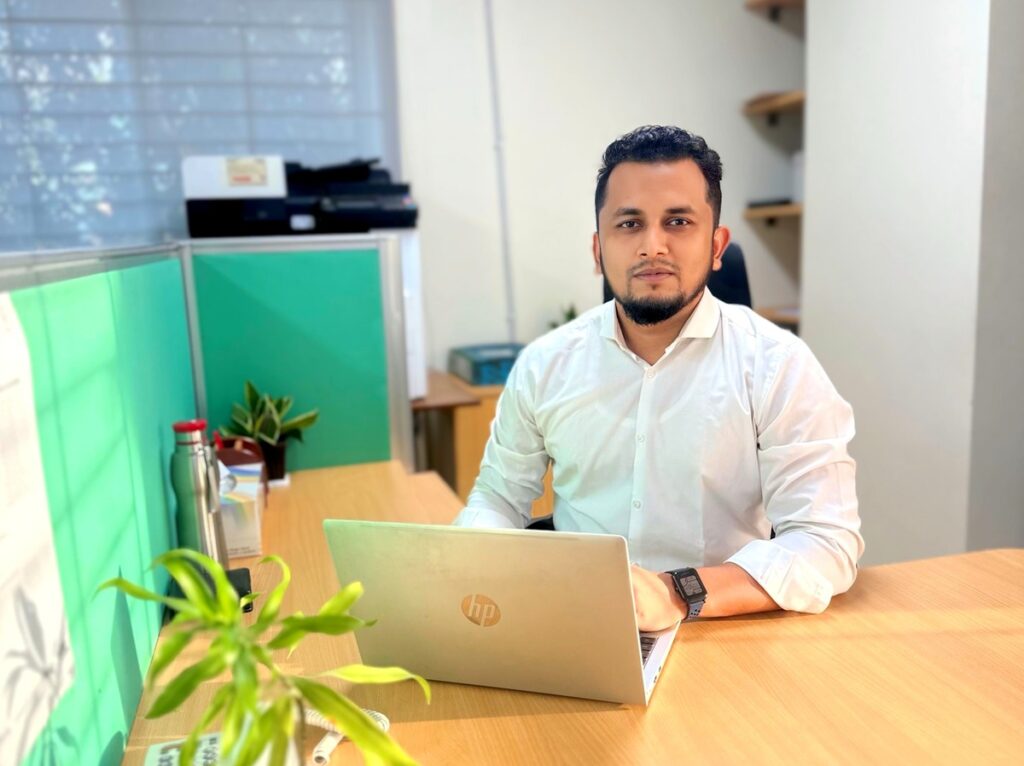
Can you please share a specific example of a challenge you faced in the chemical industry and how you overcame it?
Certainly. Although it has been crossing five years, the COVID-19 pandemic presented unprecedented challenges for the distribution team. One of the most significant challenges we faced was the disruption of logistics and transportation networks due to lockdowns and restrictions. This led to delays in the delivery of raw materials and finished products, impacting our ability to meet customer demand.
During the early stages of the pandemic, strict lockdown measures were implemented, which severely restricted the movement of goods. This resulted in delays in receiving raw materials from our suppliers and difficulties in distributing finished products to our customers. The uncertainty and frequent changes in regulations added to the complexity, making it challenging to plan and execute our distribution operations effectively.
Flexibility and agility were crucial during this period. We implemented flexible working arrangements for our staff, allowing remote work where possible and ensuring the safety of our employees who needed to be on-site. We introduced transport based delivery strategy and distribution plans dynamically. Therefore we kept our warehouse & delivery staffs in safe environment rather than sending them for delivery especially for remote area delivery where staffs were needed to night stay. This agile approach enabled us to respond swiftly to disruptions and minimize delays. We implemented an optimized inventory management strategy to balance the need for sufficient stock levels with the constraints of limited transportation capacity.
This experience highlighted the importance of resilience, adaptability, and proactive planning in overcoming supply chain challenges during a crisis.
Mr. Nurul, How has your experience with Container Freight Stations and Inland Container Depots contributed to your role at Berger Paints?
My experience with CFS & ICD has significantly contributed to my current role in the distribution department. My previous role provided me with a comprehensive understanding of logistics and supply chain operations. I gained hands-on experience in managing the movement of container/goods, optimizing storage solutions, and coordinating with various stakeholders to ensure seamless operations. This foundational knowledge has been invaluable in my role at Berger Paints, where efficient distribution is key to meeting customer demands. Another vital role I was played in ex-depot that was involved overseeing container movement, equipment & transportation repairing including RST, SLT, Fork-lift operation monitoring, fleet operation, CFS/warehouse operations ensuring compliance with safety regulations. This experience polished my skills in managing large-scale warehouse activities and maintaining optimal inventory levels at my current role.

What insights have you gained from working closely with suppliers and customers in the chemical and paint sectors?
Developing strong, reliable partnerships with carrying vehicle suppliers is crucial. Reliable transportation partners ensure that our products are delivered on time, which is essential for maintaining customer satisfaction and meeting production schedules. The paint industry often experiences fluctuations in demand due to seasonal trends and market dynamics. Having suppliers who can quickly adapt to changing needs, whether it’s scaling up during peak seasons or accommodating last-minute delivery requests, is vital for maintaining a smooth supply chain. By leveraging their expertise and data, we’ve been able to design optimal delivery routes that reduce transit times and costs.
Direct interaction with customers has highlighted the importance of a customer-centric approach in distribution. Understanding their needs, preferences, and pain points allows us to tailor our logistics operations to meet their expectations better. For instance, providing flexible delivery options, maintaining clear communication about delivery times, and swiftly addressing any issues that arise can significantly enhance customer satisfaction. Balancing cost efficiency with service quality is a critical insight I’ve gained. While it’s essential to manage transportation costs, compromising on service quality can negatively impact customer satisfaction and operational efficiency. Working with vehicle suppliers has helped us identify cost-effective solutions that do not compromise on reliability or service quality, striking the right balance for optimal performance. Challenges such as delays, vehicle breakdowns, or route disruptions are inevitable in logistics. Working closely with vehicle suppliers and customers has emphasized the value of collaborative problem-solving
How do you approach balancing the country’s import and export equilibrium in your current role?
There has less contribution on country’s import and export from my current role since I’m facilitating the demand generation in current market and supply accordingly to maintain country’s demand & supply in equilibrium point.
Mr. Nurul Kabir Minar, please say something to the readers!
Embrace challenges with patience, uphold integrity, and continuously build one’s technical know-how. These qualities are crucial for success. Stay resilient, learn from every experience, and strive for excellence. Together, we can shape a promising and innovative future.
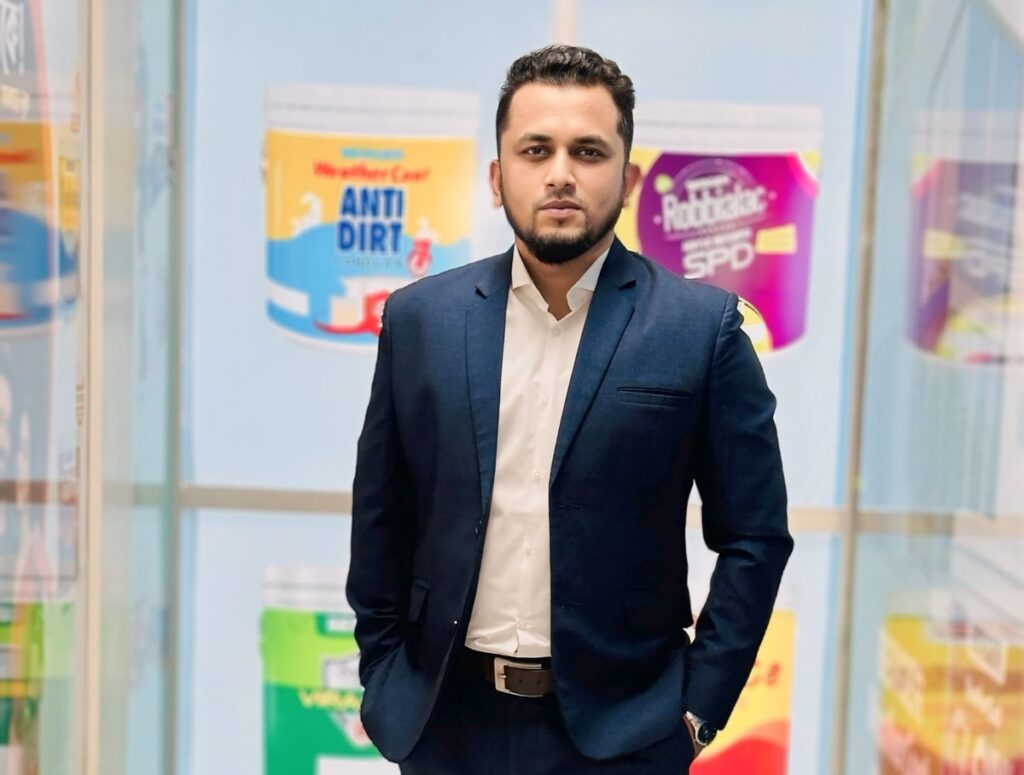
Quick Chat With Nurul Kabir Minar
The most outstanding achievement of your life as of now:
To me, being the father of baby girl is the best achievement that I received ever.
The greatest philosopher in your view:
Prophet Muhammad (SAAW)
Your Icon:
My mother, Mrs. Khaleda Begum
Name the most influential books you have read:
Al-Qur’aan
Your greatest fear:
Nothing is coming to mind right now. Only the fear is coming to mind right now is the absence of my mom.
Best piece of advice you’ve received:
Every positive people has solution for each problem and each negative people has problem for each solution.
You in only three words:
Passionate, Empathetic & Inquisitive
Skill Set
- Hard Skills: Warehouse Management System, Data Analysis, Lean Six Sigma,
- Soft Skills: Communication, Leadership, Adaptability
Prayer For The Human Civilization
In times of war and conflict, my prayer is for peace to prevail. May we find the strength to stand in solidarity, transcending boundaries and differences. Let patriotism inspire us to build a future rooted in unity, compassion, and mutual respect, ensuring a harmonious world for all.
The InCAP: Thank you, Mr. Nurul Kabir Minar! It’s a glittering conversation with you!
Mr. Nurul Kabir Minar: My pleasure! Wish you all the best! Thank you.
To read more about Professional’s stories, Please Click Here!